
Toy Safety and Quality, Inc.
Consumer, Children's, and Licensed Products
Expert support to ensure your Consumer Products are Market Ready before they are produced!
▶︎ Child Safety
▶︎ Brand Protection
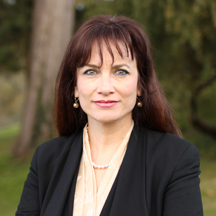
Rachel Murray Meyer
Toy Safety and Quality, Inc
San Francisco CA 94118
rachel.tsq (at) me.com
Toy Safety Tips
An Executive Summary for Successfully Bringing Toys to Market-
© Rachel Murray Meyer 2024
In the summer of 2007 millions of toys were recalled. Consumers Union labeled 2007 “The Year of the Recall”. Most of these recalls were for design related issues such as small powerful hazardous magnets and small parts in toys for children under three years old. The rest were primarily for lead. An Act of Congress, The Consumer Product Safety Improvement Act of 2008 (CPSIA) was created to address these issues. There are rules regarding the certification of children’s products, see below.
10 Tips for Brand Protection for Toys and Children’s Products
1. Commit to Safe Products throughout the supply chain, from design through Raw Materials, Manufacturing, Packaging, Distribution, and Marketing. Make sure your suppliers have proper policies and procedures in place and that they are documented.
2. Identify the Age Group your toy or children’s product is appropriate for. Proper age grading determines the design and test requirements. Especially look out for small parts, which can pose choking hazards for children under three. Visit the U.S. Consumer Product Safety Commission (CPSC) website to download the complete 2020 CPSC Age Determination Guidelines.
3. Design safety and quality into your toys. Go beyond a review of the regulations and standards. Toy concepts and designs need to be evaluated to understand if they pose any potential hazards during use and foreseeable abuse, and what is the risk of such hazards occurring. Don’t rely on Warnings.
4. Clarify that the quality and safety requirements are clear and agreed to by the manufacturer. Document the requirements and consider if legal counsel is needed.
5. Comply with the Federal Legislation of the Consumer Product Safety Improvement Act (CPSIA) and frequent the U.S. Consumer Product Safety Commission CPSIA website for CPSIA interpretations and updates.
6. Certify that your toys are safe per (CPSIA) and Rule 16 CFR 1107. See section below.
7. Stay current with the Toy Industry at the Toy Association website.
8. Research the U.S. Consumer Product Safety Commission (CPSC) website. Learn about items that are being recalled. See what consumers are saying at: https://www.saferproducts.gov
9. Play with your toys! Also, get feedback from your kids, grandkids, neighbors and your employee’s kids!
10. Improve Continuously. It’s never too late to do the right thing! Review customer and consumer feedback. Quality issues may indicate safety problems.
CPSIA and the Testing and Labeling Pertaining to Product Certification Rule 16 CFR 1107
1. Key Requirements of the CPSIA:
a) Limits the total amount of lead in children’s product components to 100 ppm
b) Reduces the limit for lead in paint and surface coatings to 90 ppm
c) A General Conformity Certification (GCC) or Children’s Product Certificate (CPC) – (see point 2. below)
d) Third party testing – look for CPSC approved labs
e) Tracking Labels for children’s products
f) ASTM F963-23, the Toy Safety Standard, is mandatory and replaces ASTM 963-17
g) Limits for certain Phthalates in certain products
2. Certifications for children’s products including toys are required. Learn about Testing and Labeling Pertaining to Product Certification (Rule 16 CFR 1107 effective date February 8, 2013), for both Importer’s of Record and Domestic Manufacturers: link
An overview of the process:
a) Representative samples are submitted for testing to a CPSC approved lab
b) Periodic Testing, at least annually, unless certain conditions met
c) A significant or Material change may require additional testing
d) Manufacturers must establish procedures to safeguard against the exercise of undue influence on a third party lab
e) Record keeping: Manufacturers must keep records for at least 5 years that include copies of the Certificates, certification test records for each manufacturing site, test results, records of material change and periodic testing and production test if applicable. Document what you do!
f) Manufacturers may indicate with a label that the product complies with a CPSC rule or ban per specific requirements.
3. Determine if testing on components (this includes paint) could be performed instead of finished products or as a way to further strengthen the quality system and ensure compliance, using rule 16 CFR 1109 “Conditions and Requirements for relying on Component Part Testing or Certification, or Another Party’s Finished Product Testing or Certification, to Meet Testing and Certification Requirements.” link
4. Learn about the mandatory Toy Industry Safety Standard, ASTM F963.23 Requirements address a variety of hazards and test methods.
Rachel Murray Meyer is a consumer product compliance consultant and the principal of Toy Safety and Quality, Inc.
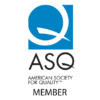

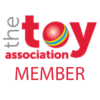
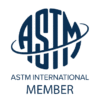
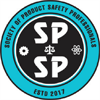
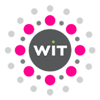